At first glance steam-energy from incinerated waste in Europe may seem worlds away from coal-energy in the Canadian prairies, however these could soon be linked by a remarkable technology that drives down carbon emissions: Carbon Capture and Storage (CCS).
CCS has application across industrial sectors and applicability around the globe as an accessible, proven technology to significantly reduce greenhouse gas emissions (GHGs) and meet international climate change goals.
Three and a half years ago, the world’s first commercial post-combustion CCS facility on a power plant began operation in Saskatchewan Canada. SaskPower’s Boundary Dam 3 (BD3) lignite coal fired power plant was retrofitted with a CCS facility capable of capturing and storing up to 90% of the previously emitted CO2, making it the cleanest thermal power plant in the world.
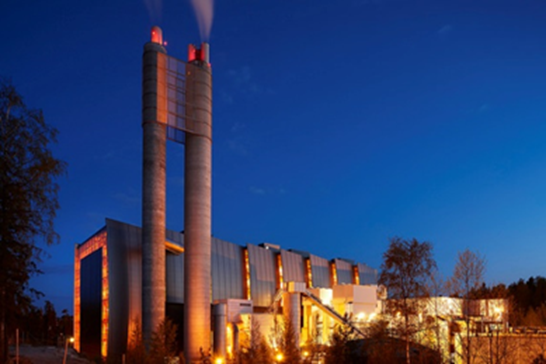
Across the Atlantic, in Oslo, Norway, the Klemetsrud Waste to Energy Plant generates electricity and district heating steam from the incineration of household and industrial waste as part of the cities integrated solution for energy recovery and waste recycling and processing. Although this is a dramatic positive contrast to the landfills that are used extensively in Canada, it still is producing about 300,000 tonnes of CO2 a year. The City of Oslo has set an emission reduction goal of 50% by 2020 and 95% by 2035.
With these emission targets in mind, the Carbon Capture Oslo project is preparing to take the next step in deploying a full-scale capture plant, by pursing support to complete a Front-End Engineering Design (FEED) study. In preparation for their project, the technical team is working with the International CCS Knowledge Centre to garner critical learnings from our operational expertise.
Canada Supporting Norway
Recently, we spent three intense days in a workshop with technical representatives from the Klemetsrud waste to energy plant on CCS experiences at BD3. This was important to Klemetsrud as the visitors could review an implementation of the specific technology that they have selected on a real plant that has over three years of operational history. The value of walking through an operating plant and seeing it first hand is hard to measure.
“Learning from the experience of others is the most powerful, yet cost-effective risk mitigation measure for any project.” – Espen Berg, Project Manager
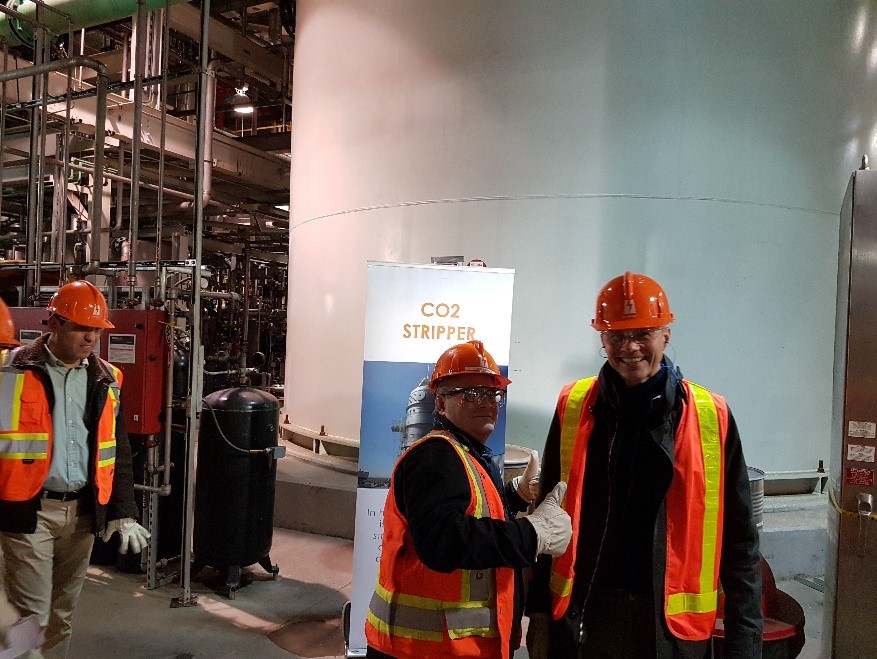
Sharing the Technical Expertise
- an in-depth tour of both the carbon capture facility, and the power plant;
- transfer of learnings from the project and the operating team from all project phases:
- feasibility and FEED,
- project execution, construction, commissioning, and transition to operations, and
- on-going operating of the facility as a commercial enterprise;
- items impacting BD3 CCS dispatch and plant output including:
- market demand,
- value for emission reduction, and
- outages, de-rates and capacity limitations;
- a review of ongoing operations cost impacts including:
- quantity of makeup chemicals,
- plant parasitic loads,
- operations staffing requirements, and
- plant technical support equipment and staffing;
- an examination plant emissions data, and testing methodologies used;
- a review of plant health and safety plans and impacts; and,
- a critical equipment inspection and operational experience review.
Importance of BD3 Evolution to Success
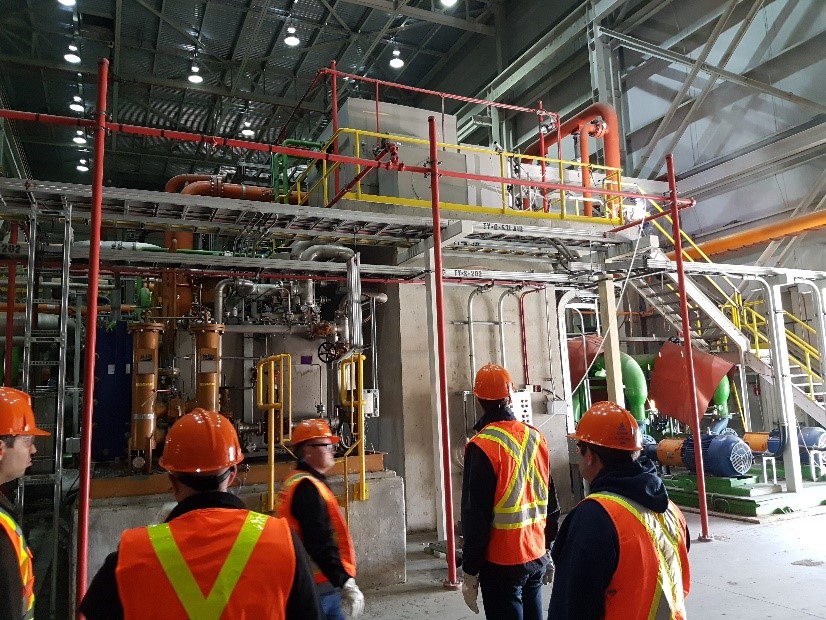
For the team from Olso, the ability to pull live and historical data from the plant’s control system historian, substantiated BD3’s evolution to success.
The beauty of it is that we have instant access to 3.5 years of real operational data that we use to troubleshoot and optimize the plant. We are, therefore able to leverage this same information to inform ourselves and others on the realities of commercial carbon capture as we strive to increase the efficiency and reduce the cost of capture for future projects.
This hands-on review of the operational data – on how the plant operates on an ongoing basis, as well as investigating start-up, shutdown and upset conditions confirmed for the Klemetsrud project team – that despite the sometimes negative public commentary – the plant is running and the plant operation, including reliability, is improving. In fact, as of April 2018, the plant has seen a 4.5 month production run being available 98.8 per cent of the time.
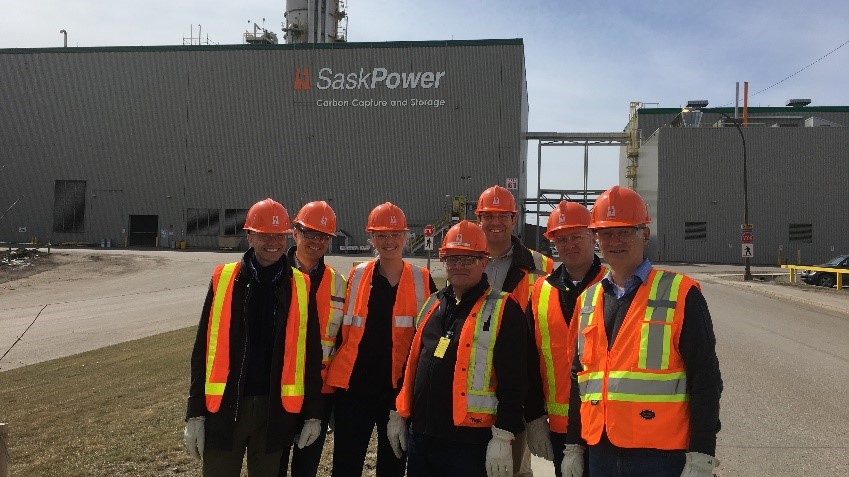
In addition to the technical review, the site tour and lessons learned for Boundary Dam 3, the International CCS Knowledge Centre facilitated discussions on trends and learning from other projects that might be applied to the Klemetsrud project.
The workshop with colleagues from Norway was a great success. Taking the time to do an extensive review of the actual plant operating data was important to Klemetsrud as it allowed their technical team to assess the plant operation and form their own conclusions. As well, I gained a huge understanding on waste-to-steam-to-energy and I am a firm believer in the relevance of sharing knowledge and the value that CCS adds to any industry.