Application of large-scale carbon capture and storage (CCS) to decarbonizing energy-intensive processes and industries responsible for 1/3 of annual global greenhouse gas emissions is gaining momentum to meet the goals of the Paris Agreement. This includes the cement industry. While learnings from carbon capture technology can be transferred from its application in capturing carbon dioxide (CO2) emissions from coal, there are a number of unique challenges to consider. One of the solutions of which, can be found in using waste heat energy.
As the main ingredient in concrete – the most widely used construction material in the world – process emissions from cement production are a major contributor to climate change. According to the International Energy Agency, the cement industry currently represents about seven per cent of the CO2 emissions globally and is the third-largest industrial energy consumer.i Despite significant improvements in efficiency, cement related emissions are expected to increase by 260% throughout the 1990-2050 period.ii
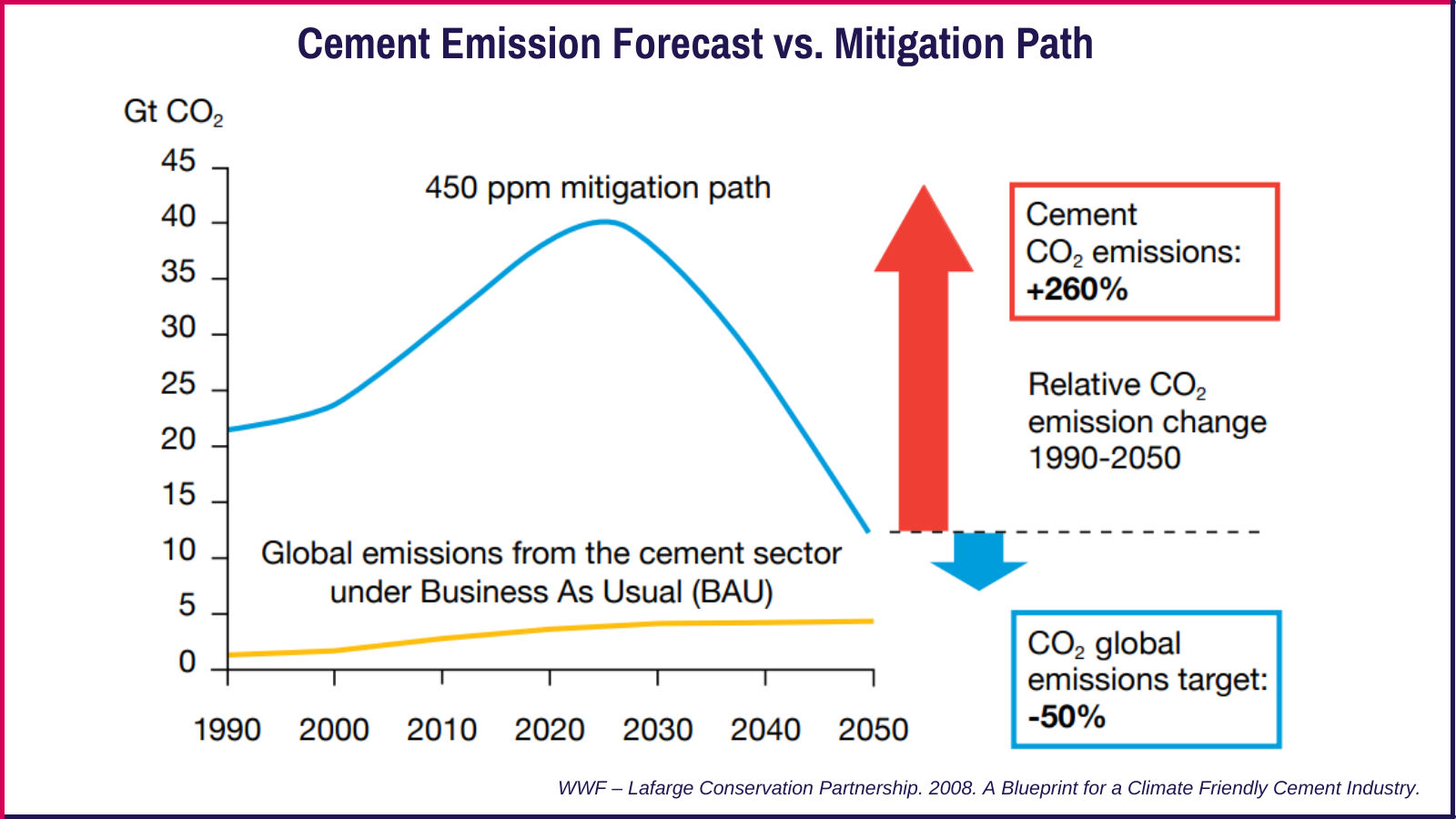
Cement is used to make concrete, the second most-consumed material in the world (next to water) and the world’s most consumed man-made material. With annual global production of cement being more than four billion tonnes, the CO2 emitted from cement production accounts for approximately eight percent of global CO2 emissions. iv
According to the International Energy Agency’s Beyond Two Degree Scenario, annual cement emissions must be reduced by at least 16 per cent by 2030 to bring the sector in line with the climate goals of the Paris Agreement.v
Post-Combustion Capture on Cement
Since around 2/3 of the total waste CO2 emissions from cement manufacturing are released in the chemical processing of raw material (limestone; CaCO3) to produce lime (CaO) – they are considered an unavoidable by-product of the cement manufacturing process that is hard to abate.vi To heat the cement kilns to the high temperatures needed, a further 40 per cent of cement emissions come from burning fuels to obtain the heat needed for the limestone decomposition process.
While cement manufacturing is an energy intensive process resulting in multiple high temperature exhaust gas streams, it does not normally produce steam, which is the thermal energy source used in the power industry for the regeneration of amine – an essential ingredient in in post-combustion carbon capture (PCC). As a result, the installation of an Auxiliary Boiler is necessary to produce the steam, and in turn energy, required for the process.
Although steam with the temperatures and pressures needed for PCC are not readily available in the cement manufacturing process – this challenge can be overcome by recovering waste heat from the cement plant to provide the energy requirements for the system, as identified in a recent study by the International CCS Knowledge Centre (Knowledge Centre) (see full paper: Waste Heat Utilization for the Energy Requirements of a Post Combustion CO2 Capture Retrofit Study of a Cement Manufacturing Facility)

Waste Heat Recovery – How it Works
Cement kiln exhaust streams from the clinker cooler and kiln preheater system contain useful thermal energy that can be converted into power.viii Waste Heath Recovery (WHR) from cement production is a proven technology that is quite common in China (more than 739 installations).ix Currently, there are a range of commercially proven and mature WHR Power Systems ranging from classic Rankine-cycle steam-based installations to Organic Rankine Cycle (ORC) configurations. While these systems use turbines to generate power, in this particular study, turbines are not required as power is not being generated. The steam produced from the waste heat recovery process is directly utilized for amine regeneration.
“Although waste heat recovery is nothing new for the cement industry, utilizing this recovery system specifically for the CCS process on the full emissions of a cement plant, has not yet been demonstrated,” says Brent Jacobs, Engineering Team Leader at the International CCS Knowledge Centre. “Our application-based research shows exactly how this this known technology can be applied to reduce the incremental energy requirements for CCS in the cement industry – a major step forward in mitigating climate change on a global scale.”
Below is a description of how this WHR System, which consists of two boilers, would function on a cement plant for the CCS process.
1. Waste Heat Recovery with Flue Gas from the Kiln
The first heat source in the WHR process with a cement plant involves the production of Flue Gas from the heating of raw material resulting in a product referred to as “Hot Clinker.” This hot Flue Gas first exits the Rotary Kiln and then passes through the Preheater Tower and leaves at approximately 400°C. Rather than the Flue Gas entering the Kiln Conditioning Tower to be cooled to around 200°C by water injection, a WHR unit can be installed in parallel to the existing Kiln Conditioning Tower to recover heat from the Flue Gas of the Preheater Tower. This parallel arrangement would allow a cement production plant the ability to operate independently of the WHR Unit, bypassing it when not in operation.
2. Waste Heat Recovery with Hot Air from Clinker Cooler
After leaving the Kiln, the Hot Clinker is put through cooling tunnels and increases the temperature of incoming air. The hot air from the Clinker Cooler is another source of waste heat that can be recovered. The air used from waste heat recovery is then fed to a Baghouse filter for particulates to be removed before it is emitted to the atmosphere.
3. Sizing Based on Beyond 90 Per Cent Capture with Optional Reliance on a WHR System
In the final scenario, the CCS plant is designed to capture CO2 from the cement plant as well as the increased Flue Gas flow from the Auxiliary Boiler when the WHR is out of service. When the WHR is in service, it is capturing beyond 90 per cent of the CO2; however, in this design case, the size of the capture plant and Auxiliary Boiler in this scenario must be larger to accommodate increased flue gas flow when the WHR is out of service.
“In order to make a decision on what option is best, technical, environmental, and economic aspects also need to be considered,” added Jacobs.
While the feasibility of every project must be assessed on a case-by-case basis – CCS technology continues to improve and evolve as a cross-cutting solution for hard-to-abate sectors. Understanding how to apply large-scale emission reduction technologies, like CCS, to decarbonize heavy-emitting industries, is a critical step in transitioning to cleaner systems. With the similarities in capturing CO2 from coal-fired power plants and cement plants, industries can continue to thrive and produce vital materials for the global economy while reducing their carbon footprint.
The International CCS Knowledge Centre is working on a CCS feasibility study at the Lehigh Hanson cement plant in Edmonton; expected for publication in the fall of 2021.
i IEA (2018) Technology Roadmap – Low-Carbon Transition in the Cement Industry. Paris, France: IEA. https://www.iea.org/reports/technology-roadmap-low-carbon-transition-in-the-cement-industry
ii WWF – Lafarge Conservation Partnership. 2008. A Blueprint for a Climate Friendly Cement Industry. http://awsassets.panda.org/downloads/englishsummary__lr_pdf.pdf
iii Vattenfall AB (June 2006) Global Mapping of Industry Greenhouse Gas Abatement Opportunities up to 2030: Industry Sector Deep-Dive.
iv CICERO Center for International Climate Research. 2018. Global CO2 emissions from cement production. http://ccsknowledge.com/pub/documents/publications/2018-CICERO-Global-CO2-Emissions-From-Cement%20Production.pdf
v Based on the Beyond 2°C Scenario (B2DS) in International Energy Agency (2017), Energy Technology Perspectives 2017: Catalysing Energy Technology Transformations, Paris: Organisation for Economic Cooperation and Development/International Energy Agency, https://www.iea.org/etp2017
vi Liv-Margrethe Bjergea*, Per Brevikb . 2014. CO2 Capture in the Cement Industry, Norcem CO2 Capture Project (Norway). Available at ScienceDirect.com
vii International CCS Knowledge Centre. 2021. Waste Heat Utilization for the Energy Requirements of a Post Combustion CO2 Capture Retrofit Study of a Cement Manufacturing Facility. https://ccsknowledge.com/pub/Publications/PAPER_GHGT15_Waste_Heat_Utilization_Energy_Requirements_Capture_Retrofit_Study_Cement_Facility.pdf
viii ICR Research. 2016. WHR in island mode. https://www.cemnet.com/Articles/story/158776/whr-in-island-mode.html
x International CCS Knowledge Centre. 2021. Waste Heat Utilization for the Energy Requirements of a Post Combustion CO2 Capture Retrofit Study of a Cement Manufacturing Facility. https://ccsknowledge.com/pub/Publications/PAPER_GHGT15_Waste_Heat_Utilization_Energy_Requirements_Capture_Retrofit_Study_Cement_Facility.pdf
xi Liv-Margrethe Bjergea*, Per Brevikb . 2014. CO2 Capture in the Cement Industry, Norcem CO2 Capture Project (Norway). Available at ScienceDirect.com