What We Do Best
We provide independent, expert advisory services for CCS/CCUS projects across heavy-emitting industries based on our team’s unparalleled experience developing the world’s first fully integrated post-combustion CCS facility on a coal-fired power plant.
Using the latest knowledge and lessons learned from major projects across the globe, we have a proven track record of helping our clients across industries lower costs, reduce risks and improve their CCS performance across technology platforms. By acting as neutral and trustworthy advisors, we help our clients successfully navigate the myriad technical, economic, policy and stakeholder complexities that accompany the development of major CCS projects and are uncharted territory for many.
Project Development and Technical Services
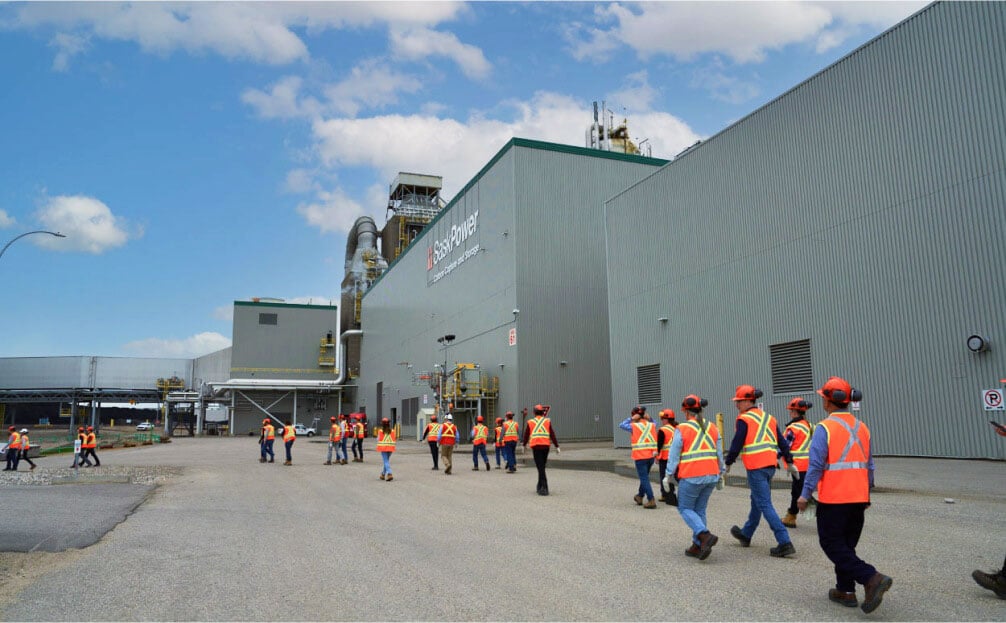
Our technical team includes engineers, chemists and process specialists who have a deep understanding of the complexities of large-scale CCS projects grounded in their unique experience working on SaskPower’s Boundary Dam Unit 3 CCS facility (BD3) near Estevan, Saskatchewan.
Our tours and customized workshops focus on the application of the significant learnings from BD3 to help your organization understand the CCS project journey through planning, development, execution, and operations. The BD3 CCS facility has been operating since 2014 and has captured and safely stored more than 6 million tonnes of CO2.
Our experts also provide a wide range of customized support and technical advisory services to meet the needs of each client. By leveraging the knowledge and experience from BD3 and other major CCS projects, we have completed comprehensive feasibility studies for second-generation CCS projects, and we are supporting a wide range of clients with services including: